W tym artykule dowiesz się jak wygląda praca konstrukcyjna nad jednym z najnowocześniejszych instrumentów muzycznych – syntezatorem firmy Polyend.
Kilka lat temu Piotr Raczyński współtwórca firmy Polyend postanowił, że przekuje swoją pasję do muzyki w biznes. Pierwszym instrumentem startupu został słynny automat perkusyjny. Ochrzczono go Perc. Jest to automat perkusyjny uderzający w werbel lub jakikolwiek inny przedmiot generujący dźwięk. Zaletą jest to, że dźwięk nie jest generowany z trzewi rezystorów, tylko fizycznie, poprzez uderzenie urządzenia o przedmiot. Równie dobrze może być to garnek po niedzielnym rosole jak i warta kilka tysięcy złotych profesjonalna stopa. „Chciałem kontrolować cyfrowo urządzenie, które uderzałoby zupełnie fizycznie w perkusję.” wspomina w jednym z wywiadów założyciel Polyend.
Firma ma już na koncie instrumenty, dzięki którym twórcy zdobywali największe nagrody muzyczne. Hildur Guðnadóttir otrzymała Oscara za muzykę do „Jokera” w 2020, tworzoną z pomocą instrumentów Polyend.
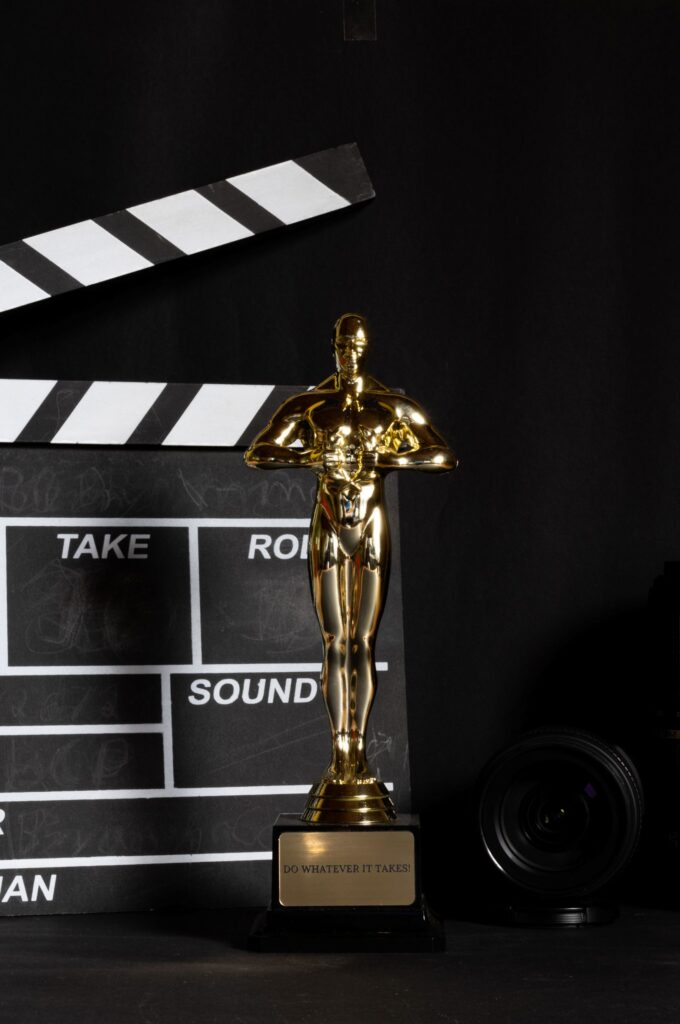
W robocie perkusyjnym nie mogliśmy za wiele pomóc, bo był to bardziej mechaniczny instrument niż elektroniczny. Natomiast w syntezator Medusa i w Poly, która tłumaczy cyfrowe komunikaty MIDI na analogowe, mogliśmy już wejść znacznie szerzej.
Z olsztyńską firmą pracujemy od 2019 roku. Na podstawie tej kilkuletniej współpracy, przedstawimy Ci w trzech krokach jak wygląda tworzenie z nami nowego projektu od zera.
1. Stworzenie prototypu
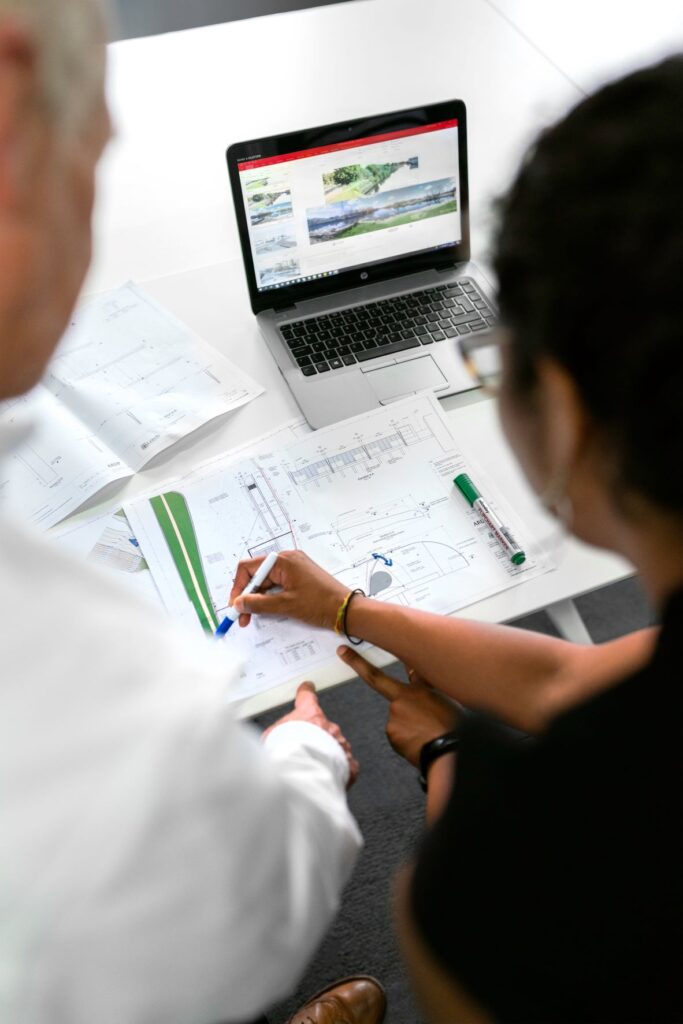
Wiedzieliśmy, że konieczna będzie bliska współpraca z twórcami urządzenia, z jego projektantami, testerami.
W olsztyńskim biurze pracuje zespół konstruktorów, grafików i elektroników, który tworzy liczne projekty i kolejne wersje tak, by w końcu stworzyć prototyp, który można poddać ostatecznym testom.
Michał Piłat tworzy płytki drukowane. To te, najczęściej zielone, elementy ze ścieżkami i komponentami elektronicznymi przypominającymi miniaturowe makiety miasta. To jeden z kluczowych elementów instrumentów.
Marcin Borkiewicz jest grafikiem, który nadaje kształt wszystkim urządzeniom Polyend, instrukcjom, projektował tez całą identyfikację wizualną marki. Połączenie wizji, hardweru i estetyki dało gigantyczny sukces w branży.
Naszą rolą było stworzenie, zaprojektowanie i wykonanie padów do instrumentów.
W przypadku klawiatur silikonowych, którymi steruje się urządzeniami Polyend, jest kilka ważnych elementów. Jednym z nich to twardość silikonu. Obecnie mamy dostępnych 10 różnych twardości w skali Shore’a. Ale to nie wszystko, bo liczy się również sama konstrukcja przycisku, jego wykończenie (z kroplą żywicy epoksydowej lub nie) jak i element jaki ma się znajdować pod klawiszem – pole kontaktowe, membrana, microswitch.
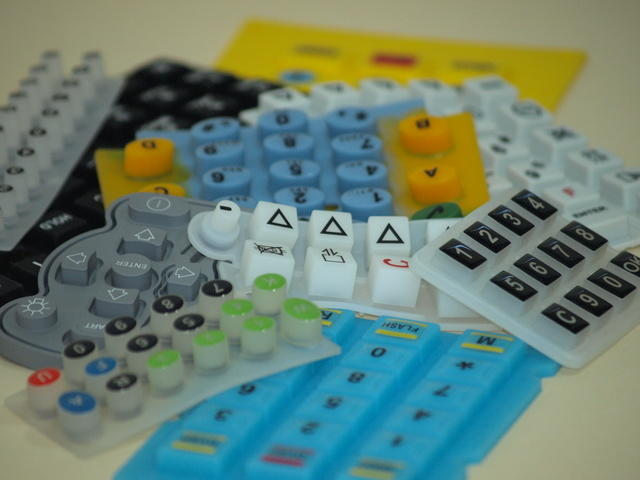
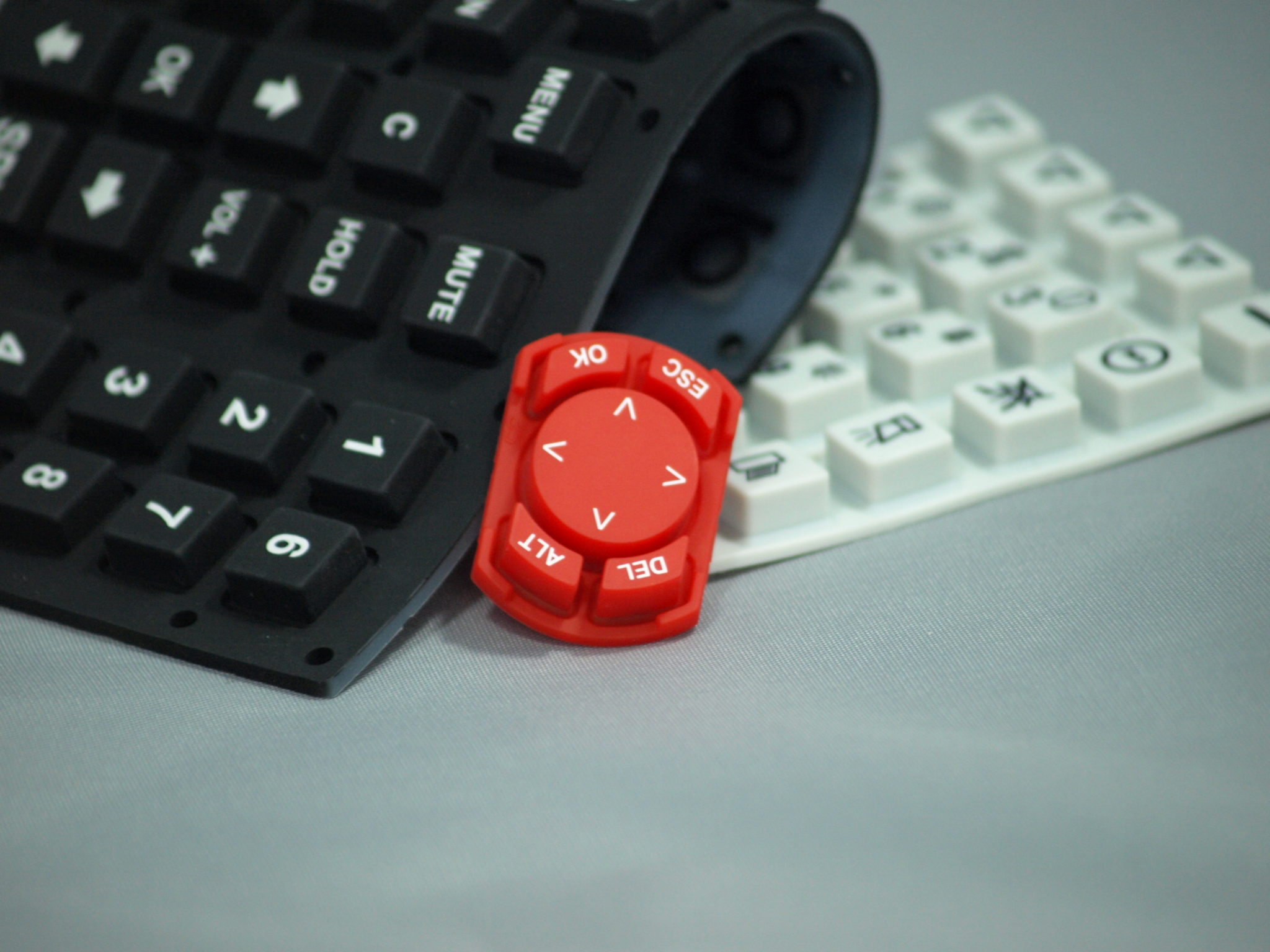
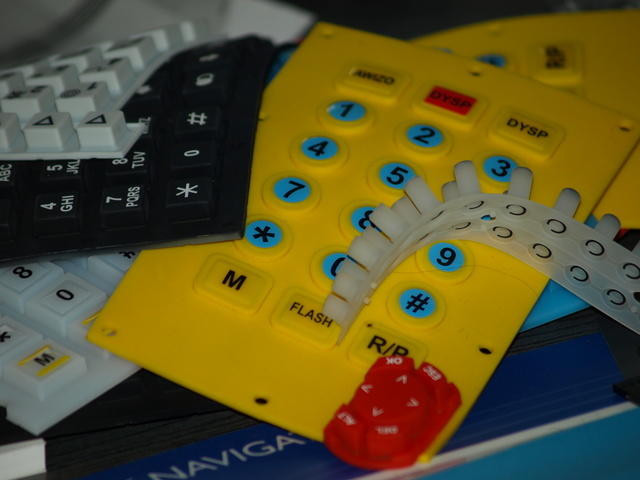
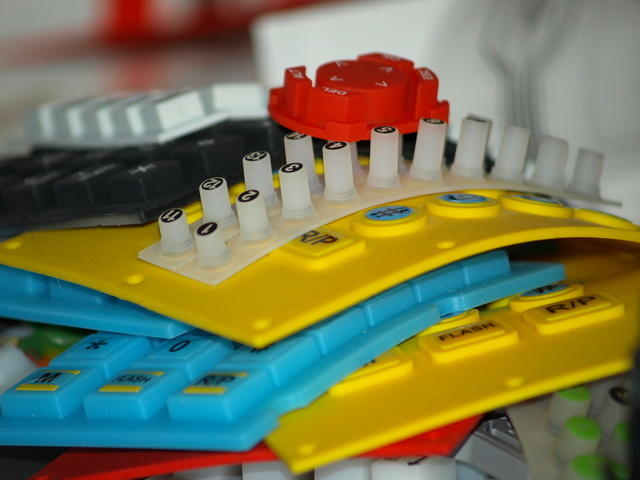
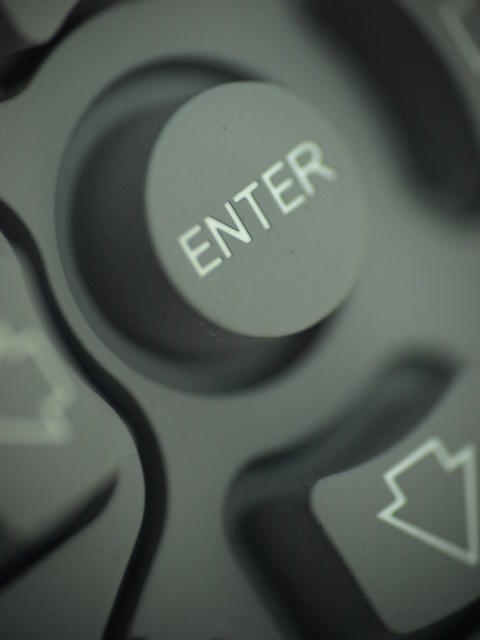
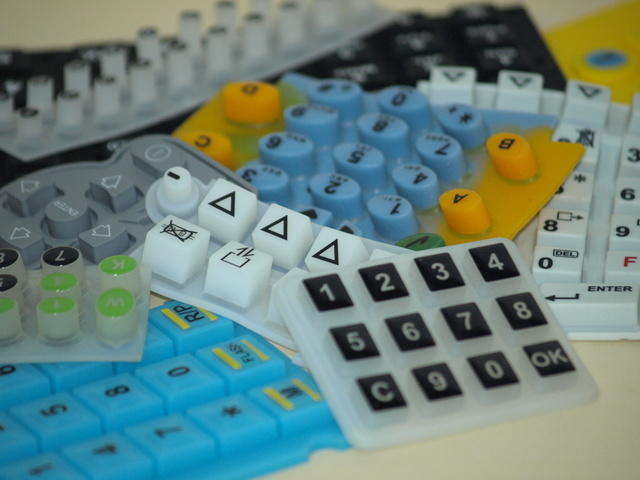
Innym kluczowym elementem był dobór odpowiedniego koloru silikonu, tak by stanowił dokonały dyfuzor dla światła diody, która podświetla cały pad. Ważne było aby podświetlenie rozprowadzało się równomiernie i nie mieszało się z kolorem z sąsiedniego pada. Każdy pad może być wszak w innym kolorze.
2. Wykonanie próbek
Odpowiedni dobór wszystkich tych parametrów jest kluczowy do tego, aby klawiatura i jej przyciski działały zgodnie z założeniami konstruktorów. Niektóre z tych elementów można zmienić w fazie produkcyjnej – np. twardość silikonu, natomiast niestety zmiana mieszka, czyli skoku klawisza, nie jest możliwa bez wykonania nowej formy. Takie zmiany są bardzo kosztowne.
Dlatego w tym przypadku, tak kluczowa była dobra komunikacja i dobranie materiałów, aby efekt końcowy był zgodny z założeniami. Przygotowaliśmy w sumie 10 próbek z różną twardością silikonu, dobierając różne parametry.
3. Testowanie
Następnym krokiem było wykonanie testów.
Całe szczęście Olsztyn nie jest daleko od Warszawy dlatego, Tomasz, doradca techniczny i konstruktor, kilka razy odwiedził stolicę Warmii i Mazur.
Takie wizyty zawsze dają dużą wartość, ponieważ to co tworzymy ma być używane przez człowieka, a więc liczy się bardzo sensoryka i haptyka, czyli wszystkie odczucia końcowych użytkowników urządzenia.
Po kilku tygodniach prób i testów, wiadomo było już z jakiego materiału, z jaką twardością i w jakim kolorze powinny być ostateczne pady. Dzięki bliskiej współpracy mogliśmy wyprodukować ponad 50 tysięcy sztuk padów, które pracują na całym świecie.
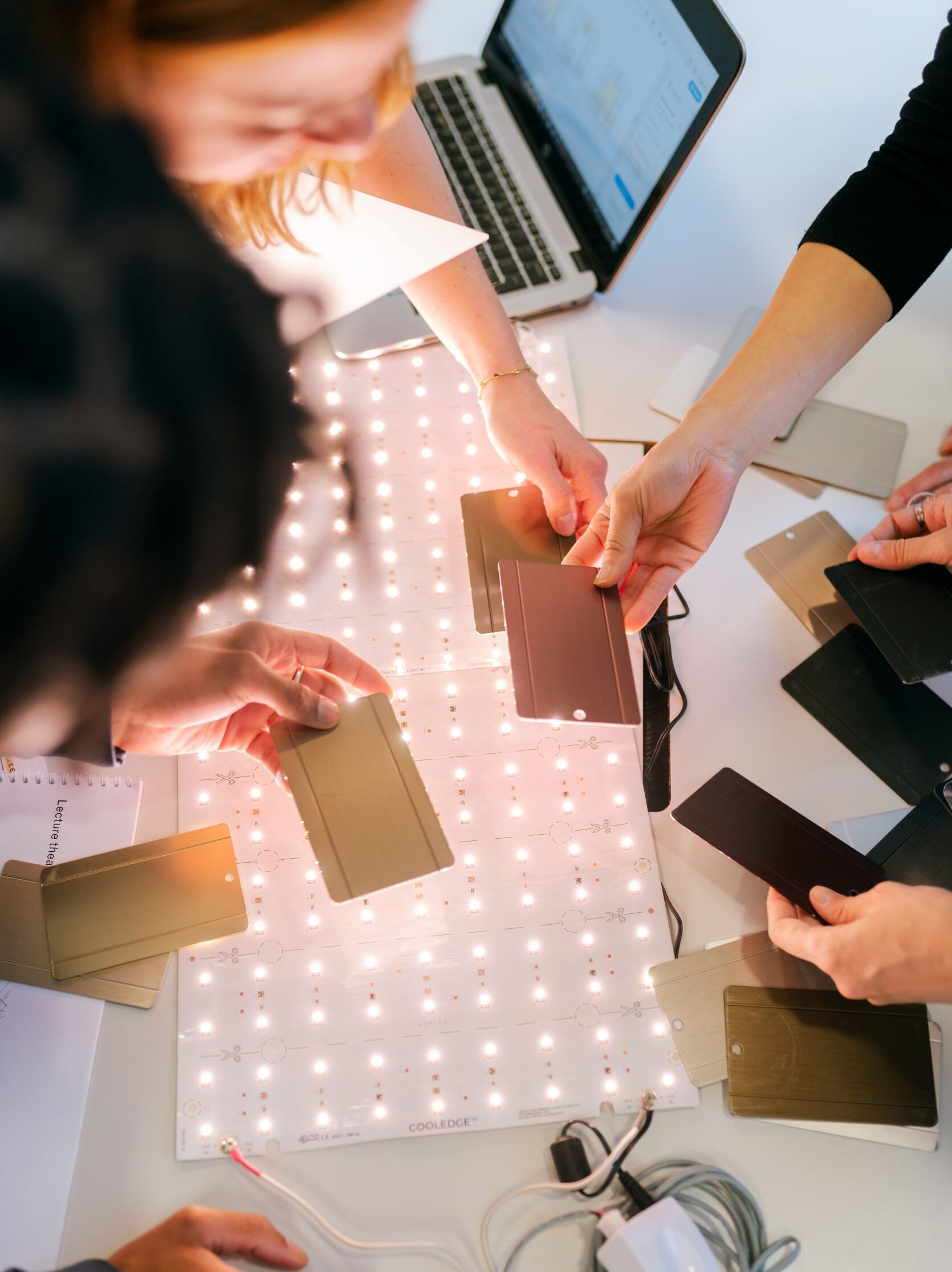
Jasny i przejrzysty proces, który jest przedstawiany na początku współpracy w każdym projekcie, sprawia, że klient na każdym z etapów jest świadomy co się dzieje, a my możemy rzetelnie wykonywać swoją pracę. Dodatkowo pozostawanie do dyspozycji klienta, a nieustanny kontakt na każdym kroku, od złożenia zamówienia, po dostawę, a także po wykonaniu zlecenia, gwarantuje najlepsze rezultaty. Ostateczny produkt nie jest kotem w worku, tylko dopracowanym w każdym szczególe komponentem, na który klient ma realny wpływ w trakcie produkcji.
Użyte zdjęcia są autorstwa:
1.Michał Karoń z Pixabay https://pixabay.com/pl/photos/muzyka-mix-konsola-radio-d%c5%bawi%c4%99k-590009/
2.Mirko Fabian: https://www.pexels.com/pl-pl/zdjecie/ciemny-uroczysty-przemysl-los-angeles-11702566/
3. ThisisEngineering RAEng on Unsplash https://unsplash.com/photos/SyRlD4s_amw
4. LC Elektronik
5. ThisisEngineering RAEng on Unsplash https://unsplash.com/photos/Ab1CJDxlnOM
PRZECZYTAJ TEŻ :
Masz pytania? Porozmawiajmy co możemy razem zrobić.
Napisz do nas! Odpowiemy w przeciągu 48 godzin