Turn your invention into a shippable product!
Combine your electronic with our housing solutions. Send us a briefProcess flow
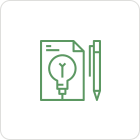
Get a technical project
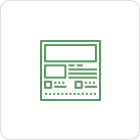
Validate your prototype
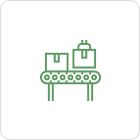
Order serial production
One Stop Shopping
we offer customized enclosures and user interface technologies for front and side electronics. All in one easy stop
Built in few weeks
combine your electronic project with our solutions – save time and money to reach your market soon
No minimum orders
all orders have same priority whether it’s a single piece for a one-off project, or a production run of thousands.
What we value
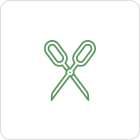
dedicated projects
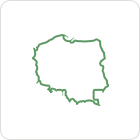
made in EU - Poland
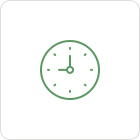
time saving outsourcing
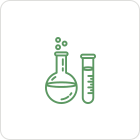