Ergonomics at a Good Price
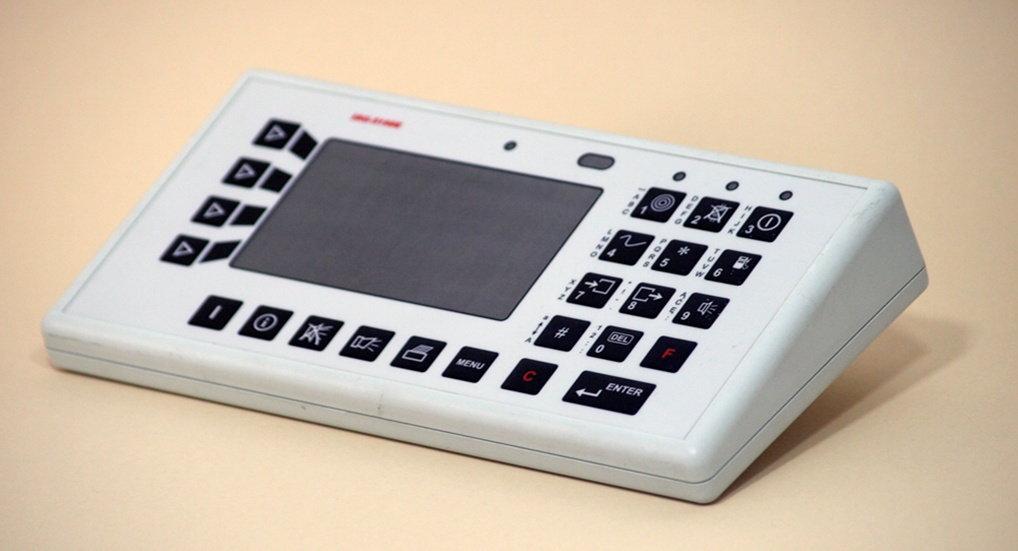
The Story
One of the Clients had a good idea for a new product. However, it was hard to predict whether the product will sell well. In addition, in the case of the traditional production, the implementation costs would be difficult to recover, if the product would require significant amendments after the initial tests.
The Solution
LC Elektronik implemented a three-step solution.
1. Firstly, a prototype and a test batch in a typical catalog plastic case have been created, a membrane keyboard was created, too. The customer received a fully functional device, which he gave later for evaluation to several operators. Then, based on tests, the changes were made. Those changes allowed for making a trial batch to be tested in real conditions.
2. Secondly, a silicone keypad has been created, which could also be used for the final product. Then a standard aluminum case has been added. It was more expensive than the plastic one, but guaranteed better resistance in the actual working conditions. The resulting comments received during testing have been used to design the final version of the product.
3. Thirdly, the injection mold has been built. After implementing modification in the software, which aim was the adjustment of the product’s functionality, the continuous production has been launched at 2,000 units per year.
The Benefits
By giving at the disposal of the customer a variety of technologies, LC Elektronik has managed to optimize the time, costs and production of the project. Custom made production with the use of the molds, even at 2,000 units per year, has proved less expensive than mass production based on ready-made catalog elements. The final product has met ergonomics requirements and the needs of the end user.
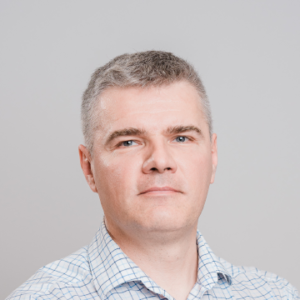
Tomasz Kamiński
Tomasz.Kaminski@lcel.com.pl
+48 22 569 53 07
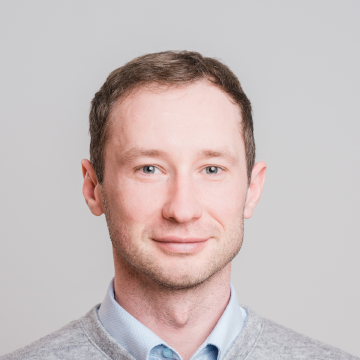
Marcin Gapisz
Marcin.Gapisz@lcel.com.pl
+48 22 569 53 11
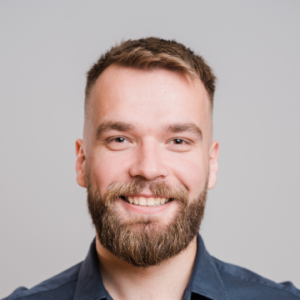
Marek Ćwikła
Marek.Cwikla@lcel.com.pl
+48 735 963 166