We have already announced a series of articles about SIT, that is how we implement this methodology to solve problems and develop our innovation. We will start the cycle with subtraction.
What is subtraction?
A technique that involves removing an essential ingredient of the product, but removing it could help in obtaining additional benefits. It is simply simplification. That’s how the Walkman was invented in this way, it is a classic tape recorder without a recording function. This technique was also used by well known Swedish furniture shop, by simplifying the assembly of its furniture and by improving packing for easier transport. This shop persuaded customers to find products themselves and take them from the shelves and assemble them at home. This significantly influenced the price of goods and the success of this company.
This SIT method shows that sometimes more comes from less.
Know how: Application of subtraction technique in LC Elektronik
In the design phase of the new membrane keypad, the customer pointed out that he cares about three elements:
- shading effect on the graphic overlay in the key area
- and a thin construction
- three LED bars with very effective light separation.
Graphic overlay – shading effect on the graphic overlay in the key area
However, while designing and estimating costs, it turned out that shading with the demand of very high resolution can’t be obtained by screen printing and this process must be complemented with digital print. Unfortunately, it was associated with much higher production costs, which the client also wanted to avoid. The expected effect was not so attractive that these costs would be incurred. That is why we gave up the shading and the imprint of the overlay was made by using the homogeneous screen method.
The design effect was very satisfying and did not increase costs unnecessarily.
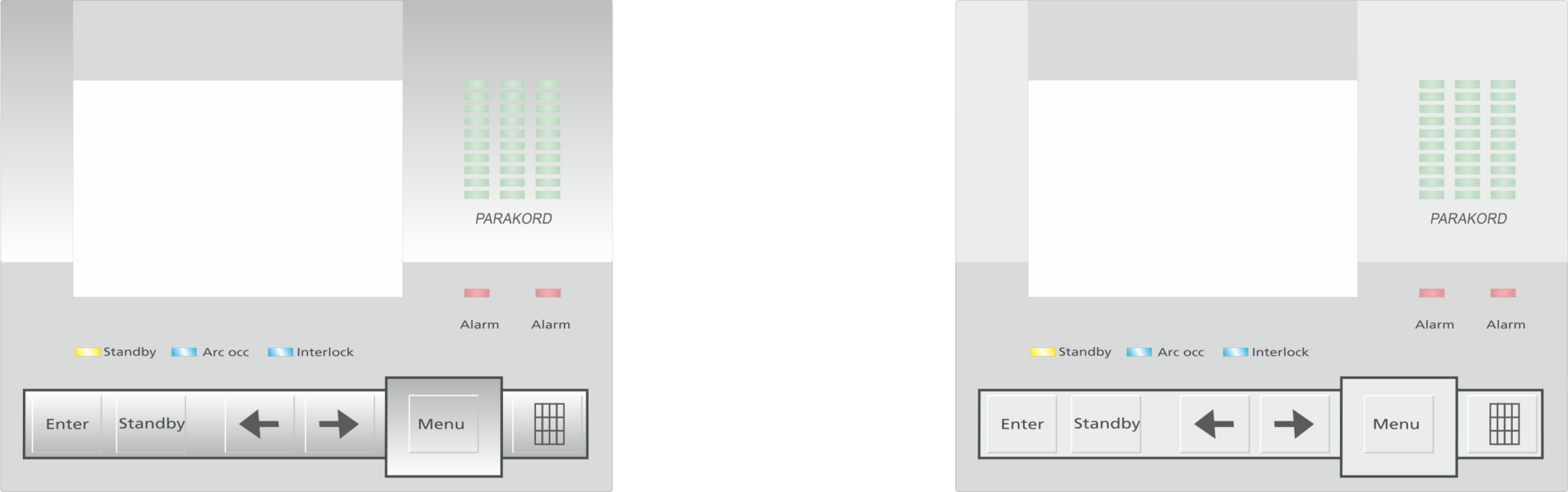
Construction and LED bars with very effective light separation
In order to achieve a proper lighting effect, a particular LED light should be well separated from each other without the side light penetration.
Usually, 1 mm aluminum sheets are used in such cases, which works well as an opaque material but would significantly increase the thickness of the keypad and would be difficult to make for precise cuts. Construction demands assembling double side adhesive spacers with a very fine cutout the pattern in LED’s bar area on both sides.
LC Elektronik proposed to remove the aluminum sheet and use a special black material with a thickness of 0.5 mm (black spacers on both sides of PMMA).
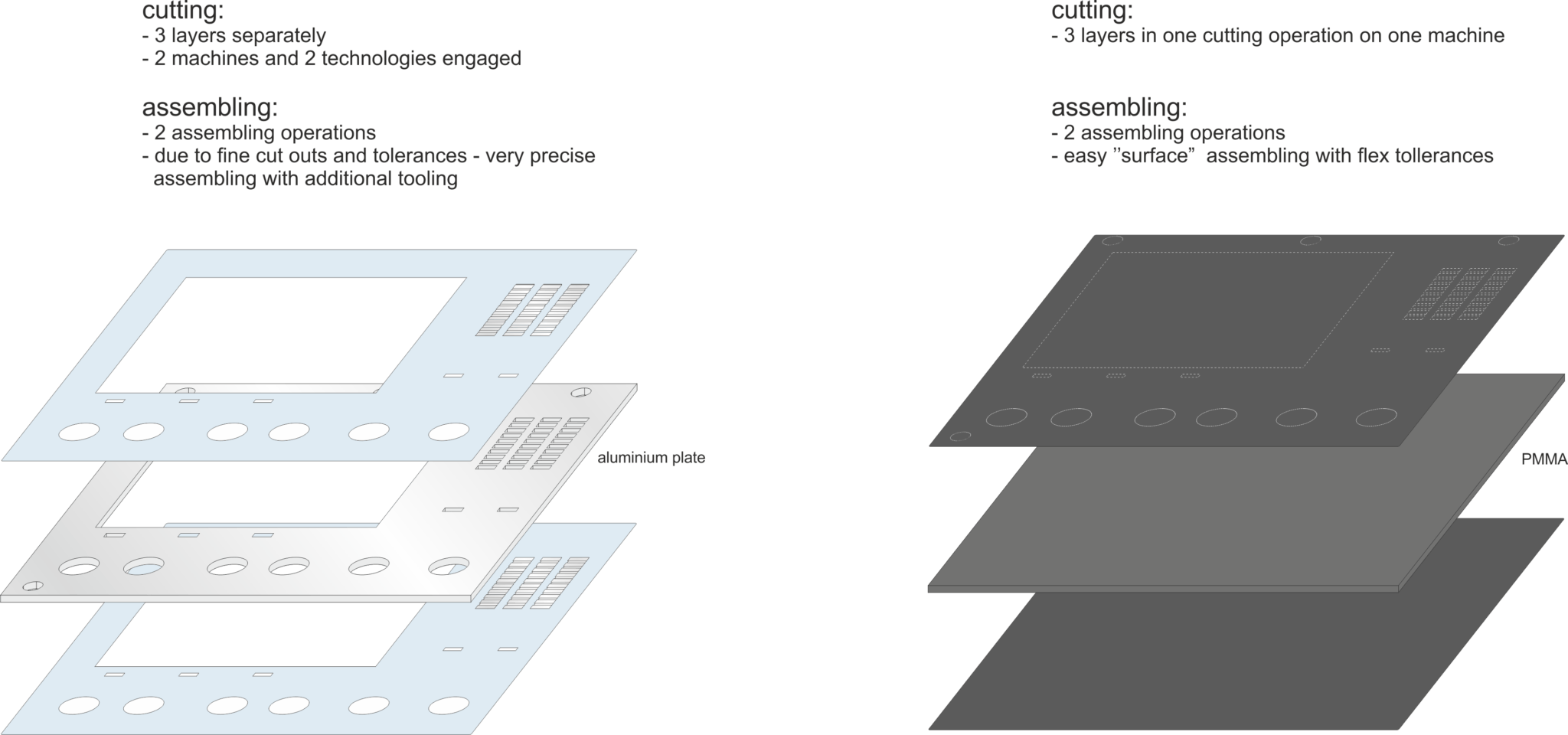
- a very simple spacer application on PMMA over the entire width
- a three-layer construction was thinner than 1 mm aluminum plate with 2 spacers by ca 0,5 mm
- three pure layers (without cutouts) could be easily assembled on the laser before machining
- the cutting operation was easier and faster, the operation was performed only once instead of three times (2 x spacers and 1 x aluminum plate).
Thanks to the subtraction technique, we not only significantly simplified the production process
but also achieved a lot – the customer and us.
First of all, we kept the construction assumptions, i.e. a thin keypad and obviously LED light
not penetrating backlighted areas to each other.
And most importantly, we obtained the desired effect without increasing costs,
we saved time for the production process, which was very important for both sides.