More than two years ago, a representative of a company that designs, constructs and builds modern luxury yachts contacted us. He wanted to buy a boat control panel. He wanted it to be reliable, to have backlit descriptions and buttons. It was also very important for the panel to match the design of the rest of the yacht. It often happens that when installing control devices from different manufacturers, they are in different colors, structures and completely different materials. Those factors can disturb the entire aesthetics.
The client knew that we have experience in this industry and we have carried out similar orders more than once. He knew, that had come to the right place.
He wanted to construct a whole family of control panels that would unify the control of a seagoing sailing yacht. It was important that all controls were clearly visible to the crew, both in full sun and at dark night. The key was to choose the structure and materials that would be resistant to weather conditions (sea water, high UV radiation, large temperature difference, wind).
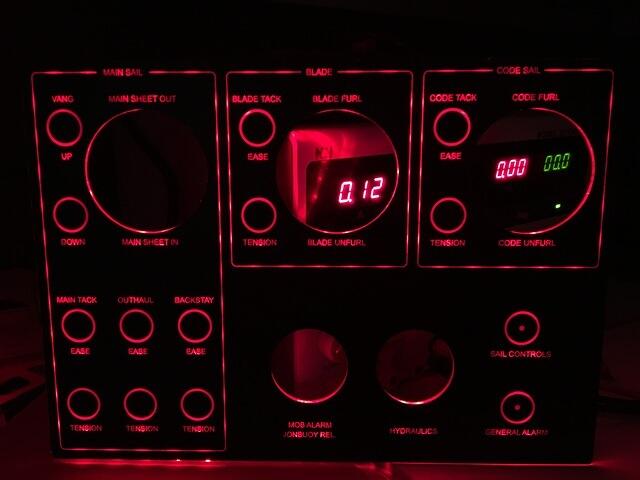
The panel according to the design for this buyer consists of 9 layers, which include, among others:
1. PCB with mounted diodes, connectors and converter.
The printed circuit board (PCB) has several functions in this case. One of them is, of course, the electronic element, where diodes or soldered connectors are mounted, but also serves as a load-bearing, purely mechanical part, which is the basis for subsequent layers. If we used a flexible printed circuit here, it would be necessary to strengthen it, e.g. with an aluminum or plastic plate.
Some of the tiles that were made for this project were made in Poland, but some of them had to be ordered in China – the largest ones were 90 × 120 cm. In all cases, the key element was the mounting of LEDs and other components not manually, but automatically. This guarantees precise assembly and long-term, trouble-free operation.
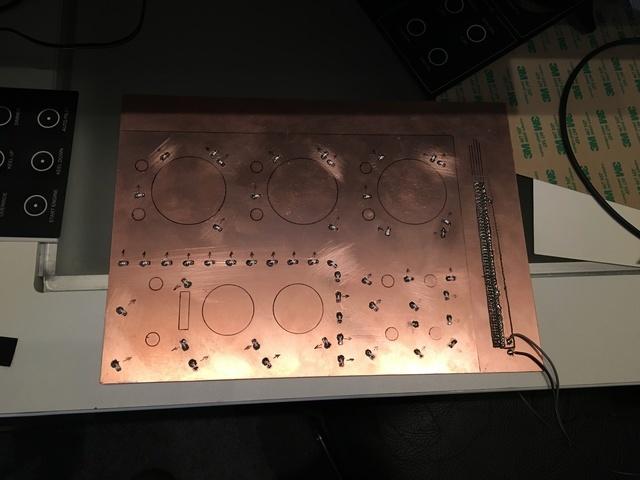
In addition to this design, it was required to create a dedicated converter that converts the voltage from 24V, used throughout the installation, to 12V, suitable for powering diodes and other electronic components on the PCB.
2. Decorative foil XE F200 with increased resistance to UV – LINK TO THE CATALOG CARD
Decorative foil is the top layer of the panel. It is this element that is most exposed to the effects of weather conditions and mechanical damage. We used Autotex® XE foil especially for this project. It is designed to work in environments with high or very fluctuating temperatures, excessive humidity and strong levels of ultraviolet light, and is ideal for both flat and embossed membrane buttons and keyboards. XE stands for extreme environment as a typical application for this material.
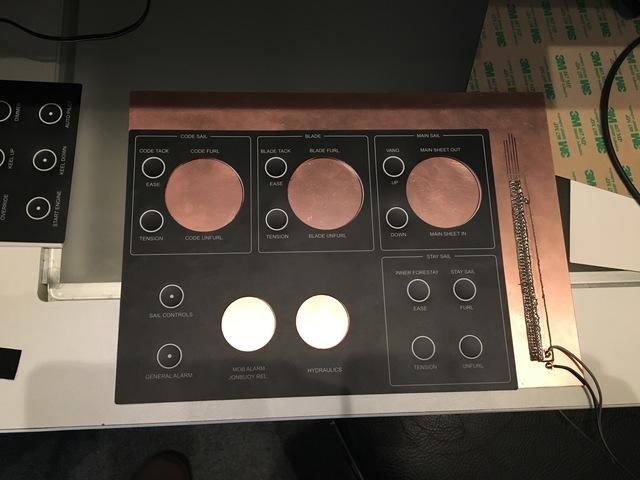
Autotex® XE is a polyester-based film with a specially constructed hard coating and backing. Unlike conventional films, which can delaminate, become brittle, peel or turn yellow due to the weather, the layers in Autotex® XE are designed to withstand ultraviolet light, moisture and extreme temperature fluctuations.
3. PMMA plate with a pattern printed in screen printing technology
Optically clear PMMA has been printed so as to be a kind of optical fiber and, at the same time, a diffuser. A diffuser for the light generated by edge and point diodes. The key to this element was the print pattern so that the final illumination effect was as even as possible. Screen printing technology, i.e. screen printing, was the best solution for this project. It is one of the older printing techniques in which the printing form is a template placed on a fine mesh. At LC Elektronik we use polyester meshes of different density, tension force and angle. Through years of experience, we have come to the point that the net stretched at an angle of 15 degrees and with a tension of 18N gives the best quality. This gives the effect of sharp and clear printing and even distribution of paint over the entire surface. This is one of the reasons why each printed form is the same and repeatable. Making a print consists in forcing the paint through the matrix with a doctor blade.
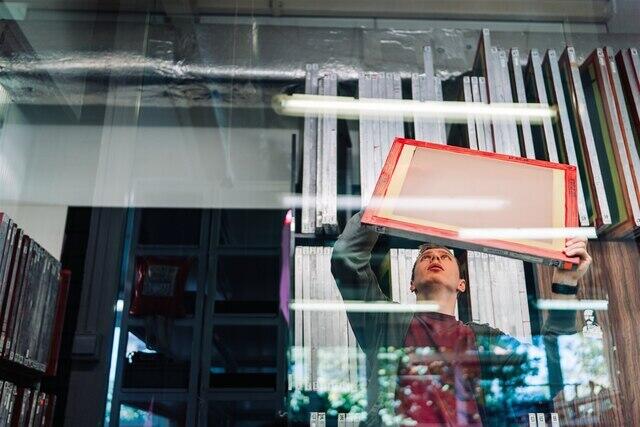
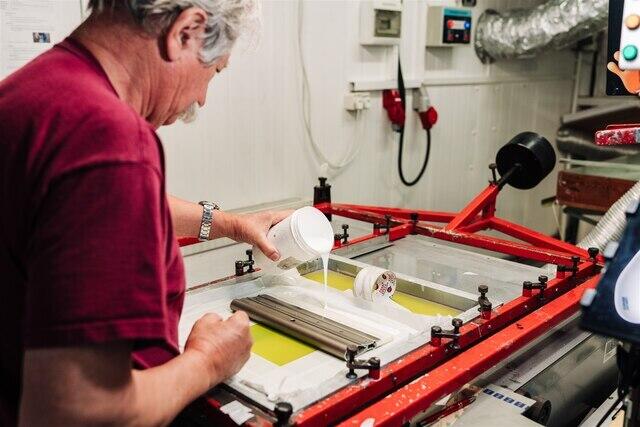
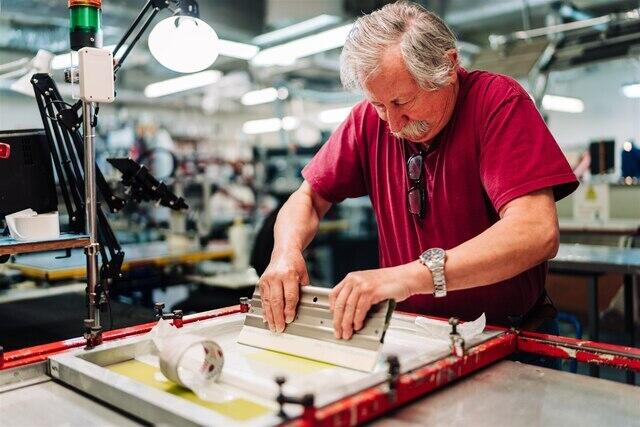
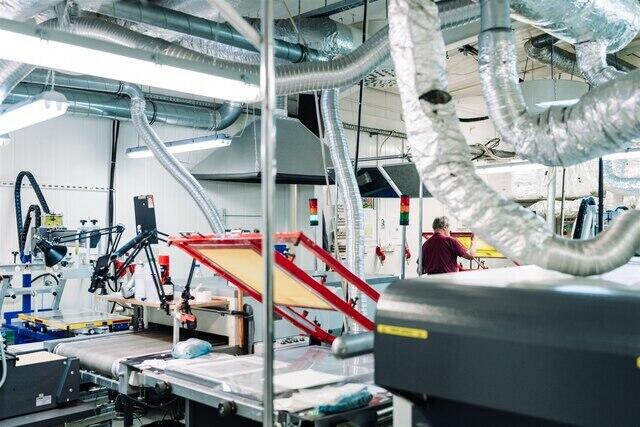
4. Several 3M 7953 specs with cutouts and thickening – LINK TO THE CATALOG CARD
For a permanent bond, all layers with integrated glue. In this project, we used only spacers from the 3M company. The spacer is a product that consists of as many as 5 layers. On both sides there is the so-called liner. A popular “silicone paper” protects glue. Now there are two layers of acrylic protective technology and a polyester film between them. This construction guarantee that the material is easy to cut by laser and is very stable, both dimensions and thickness. The glue used for this product is “200MP”, which is very popular in the membrane keypads technology. An interesting property of this is that its adhesion begins over time. This means that the longer they are stuck to the surface, the greater its strength.
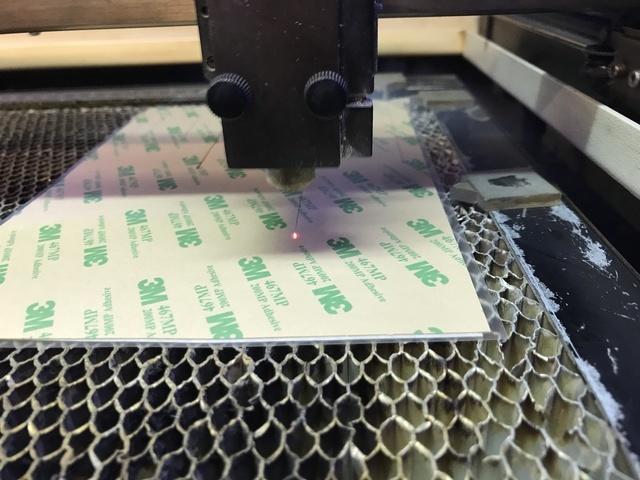
5. VHB tape sealing the whole thing – LINK TO THE CATALOG CARD
An important design project is the VHB tape. The name is English Very High Bond. The tapes are also supported by the creation of folds, complementing the list and working under working conditions. The excellent performance parameters of 3M ™ B are ensured by the use of utility tools, the technique of effective use of joining materials. In this distributor project, we have used this company to ensure, to ensure that there is a quantity in places where it should not be, and we have also aligned all e.g. with PCB tracks.
6. Light masking films
In addition to the VHB tape, other masking tapes are also necessary that have the reinforcement positioning of the entire panel. For this we used polyester films, which we additionally laminated with 3M 200 MP films.
Light is like water. If the water found any hole in the plumbing installation, you would knew this by the leak. It is the same with light. If we leave the channels, definitely the light can pass through there. It is necessary to seal the structure and block all “paths”.
7. Key tapper
From the non-obvious electrode layouts that were made, all the key tappets to work reliably and smoothly. We previously produced such elements for other projects. In this case, we used laser-cut PMMA key tappets. Additionally, the so-called The dimple, i.e. the central protrusion. The diamiters is only 5 mm and precision of 0.001 mm.
The final result
The result of our work was the achievement of quality. Thanks to the fact that they are not located in one place, and there is no such place, what device is provided on the ship. The Capitan of the yeacht in one a glance at the panel can see everything. He can be sure what kind of device or machine is on and what is its status. The Officer can concentrate on what is the key in his job – sailing.
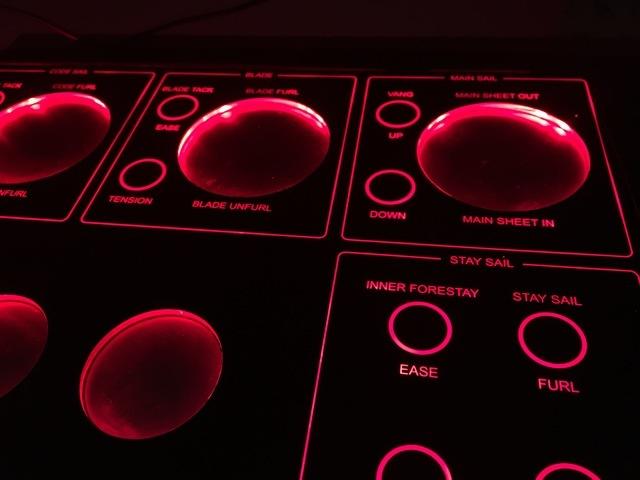
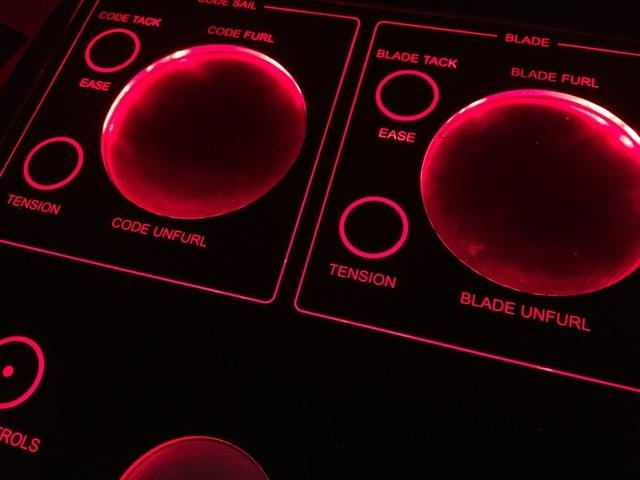
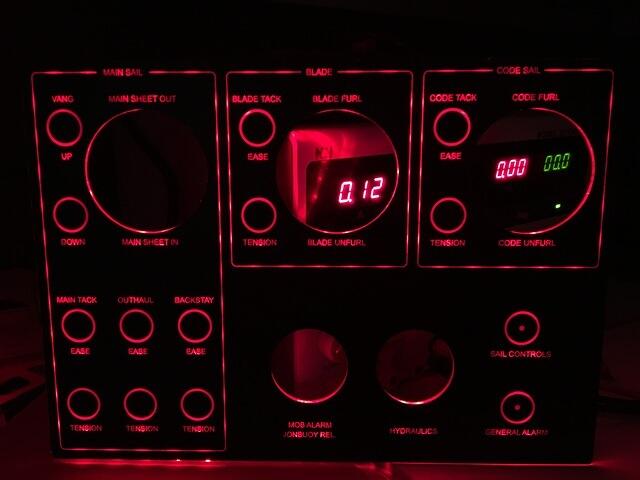
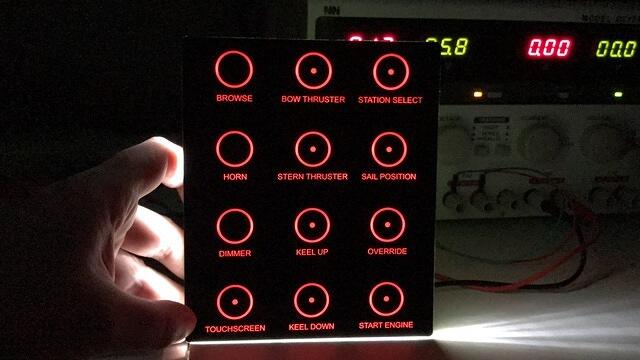
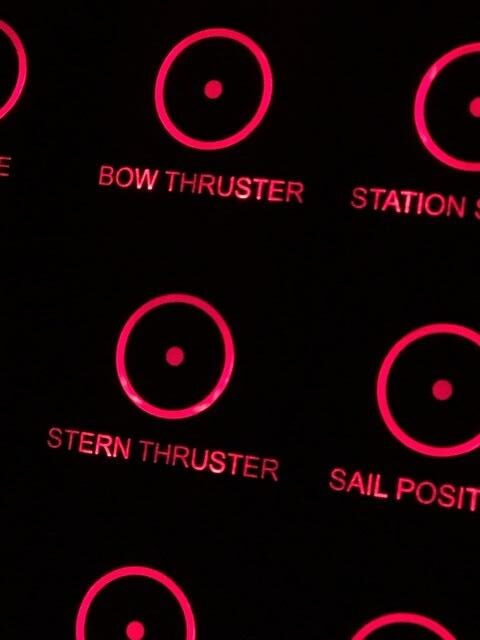
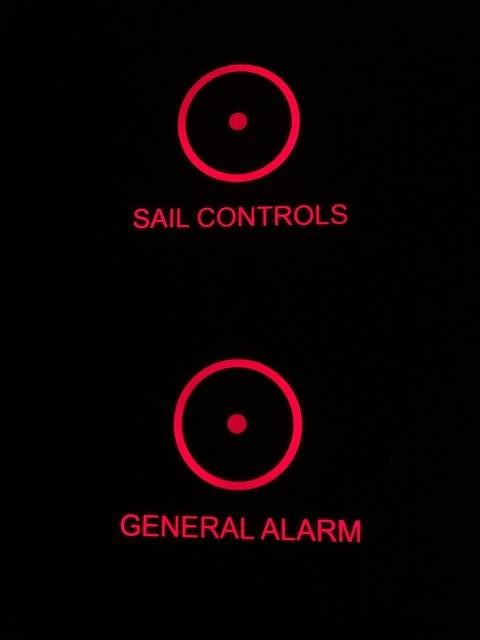
The shipowner is now not afraid that in the middle of the see his panel will break donw and he will be not able to horn or to roll up the anchor. Everything thanks to that the panels is weatherproof, the same design that the panel is simply serviced and maintenance free.
DO YOU HAVE ANY QUESTIONS? LEAVE A MESSAGE!