Application of a division technique in a company dealing in the integration of components for electronics
Divide and innovate – division technique in the SIT methodology
The division technique involves the functional or physical division of the product or its components and then redistributing it back into the product. So the division can be done in several ways, for example:
- Functional separation, by changing the position of a component, separation from the whole.
- Physical division, cutting out a component along any physical line and rearrange it.
- Preserving, dividing an item or service into smaller pieces, where each element still has all the features of the product.
For instance, the division technique was used:
– In the production of air conditioners, where the motor, fan, and hardware were separated from the original enclosure in which they used to be housed.
– Also in the remote controls devices.
– Further, the airlines used this technique, introducing on-line check-in, and fast food drive, creating separate windows to pay for a meal to increase the speed of the process.
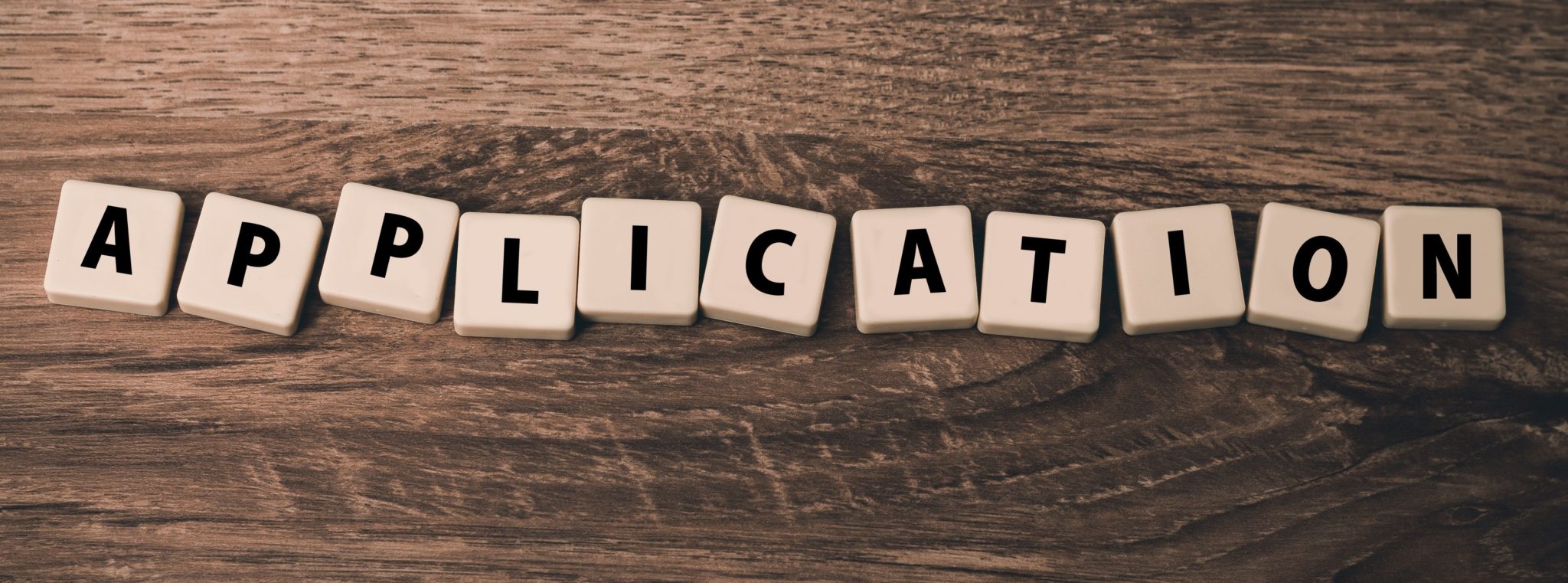
photo: Pexels
How we use the division technique in LC Elektronik
Our company specializes in integrating components for electronics, so at the beginning, it seemed to us that the use of the division technique in our company does not really apply. But it turned out that we have been using it for years.
Membrane keypad in components for self-assembly
Our customer has asked us for help in finding a solution. He needed a keypad, which would not require dismantling during servicing. It was important to him for two reasons:
- First, he was afraid of damaging the entire device. In some cases, the keypad is mounted in such a manner to the enclosure that it is extremely difficult to remove it without exposing the equipment or keypad to damage.
- Secondly, he needed the machine to work without major interruptions, because he couldn’t afford to stop working.
We found a solution very quickly. So we have created a membrane keypad in individual components for self-assembly.
The foil keypad consists of a minimum of 6 layers:
– rear adhesive
– circuit layer
– spacer
– metal dome
– metal dome layer
– spacer
– graphic foil
The first two layers – the rear and circuit layer, are permanently mounted to the device enclosure, while the rest of the layers are ordered separately. Therefore the customer can easily put together them on the site during the service.
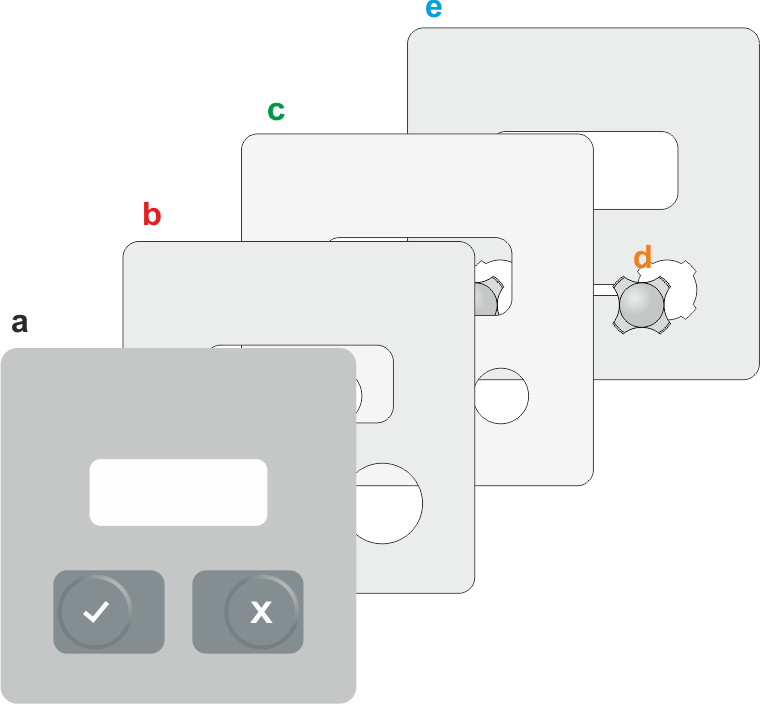
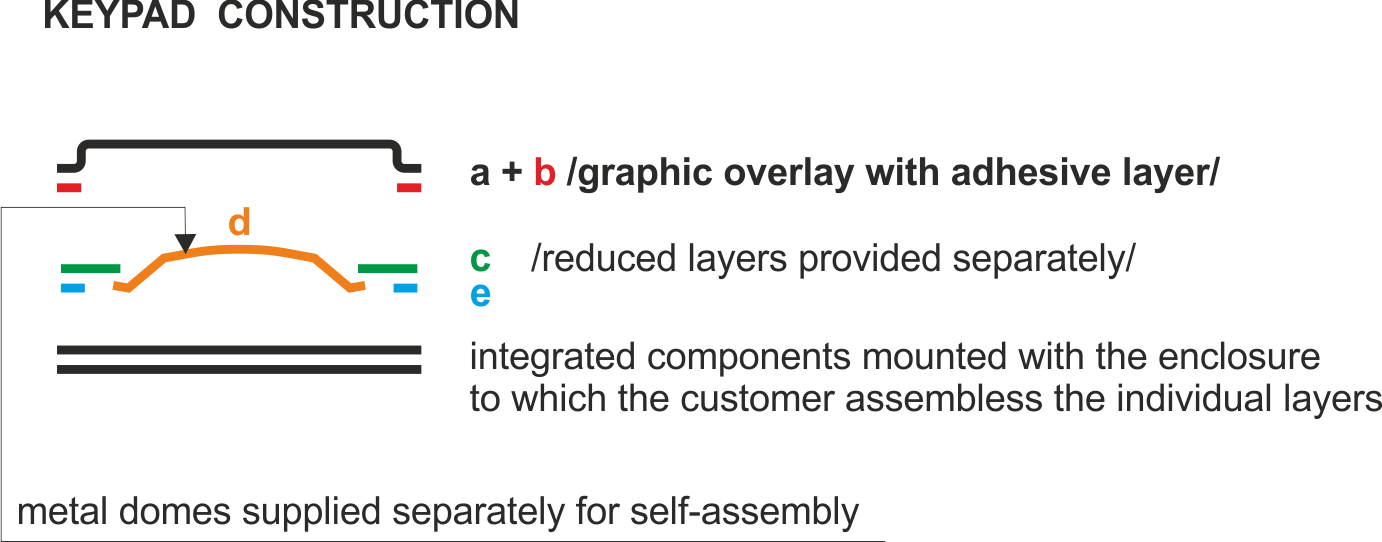
In addition the keypad from separate components also has the advantage that when the graphic foil is distorted or destroyed, we do not have to replace the whole keypad, but only the top layer.
As a result, separation of components meant that the customer is not exposed to downtime or higher costs associated with the disassembly of the whole keypad or replacement of equipment in general.
Rubber keypad – key’s configuration options
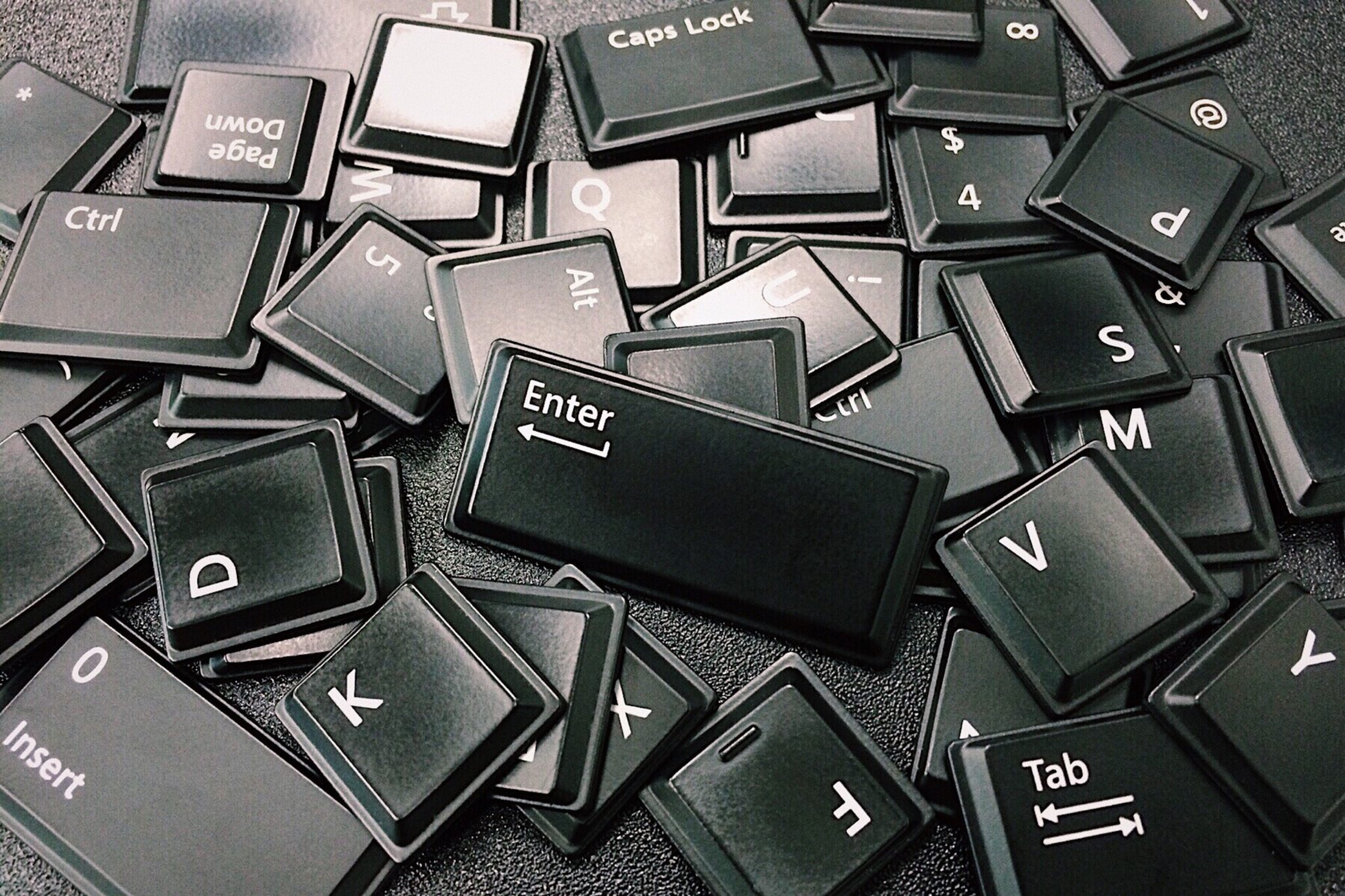
photo: Pexels
We also often use the division technique in the production of silicone keypads. Sometimes the customer needs a keypad with a specific configuration of keys for the equipment that has many details and several versions. The new mold is very expensive. So it is better to produce a keypad in a larger form or use a universal one, on which there are keys for all versions. Therefore you can use the entire keypad or make various configurations, or even cut the keypad in any way or cut off a single button. It is possible, because around every key there are channels, along the line of which you can freely cut the keypad.
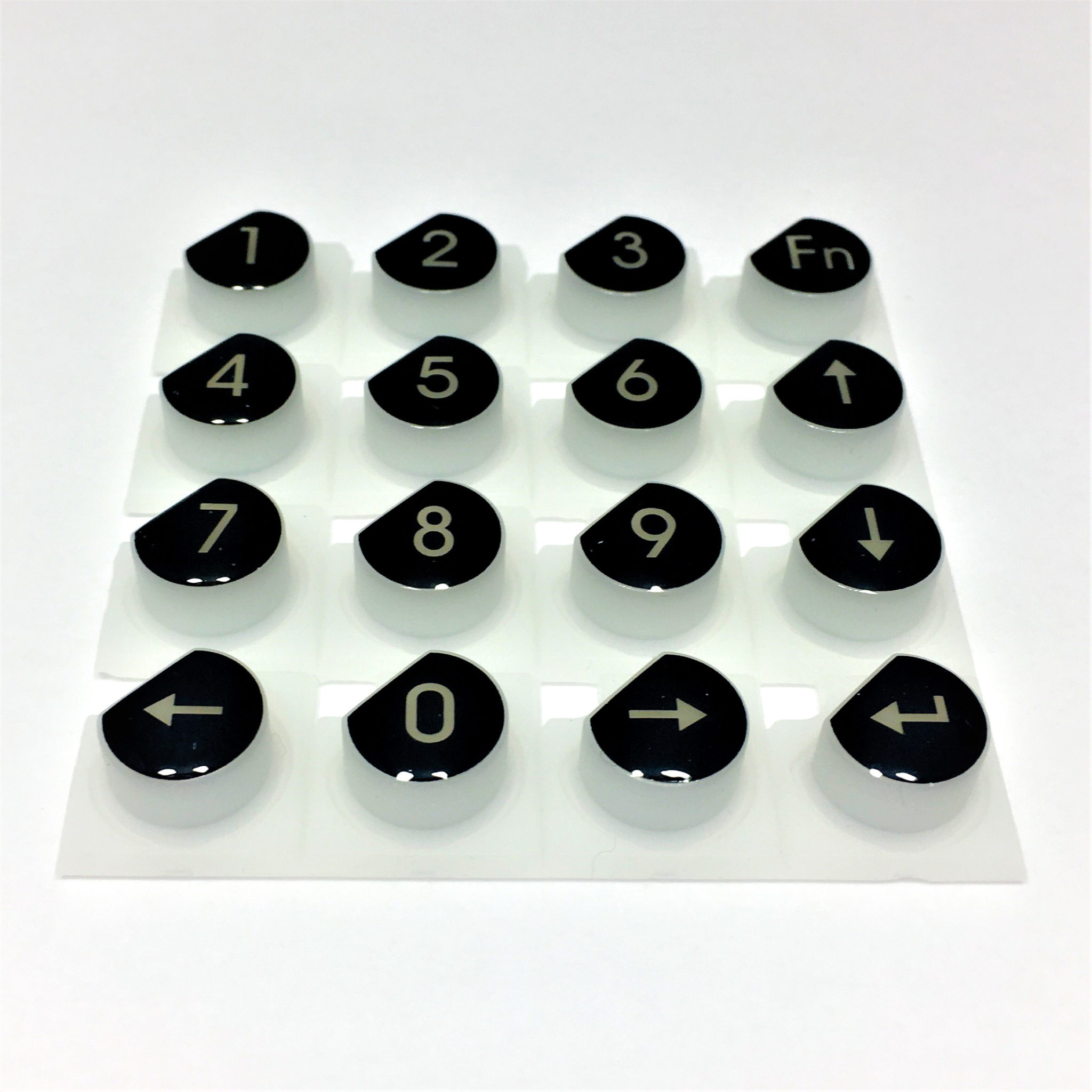
Separating part of the keypad or individual keys from the whole does not cause any loss of keypad functionality or quality at all. However, we save costs by creating new configurations and using all the keys from the mold.
Have you ever wondered if you are innovative? Have you ever used a division technique to create a project?
I’m sure you have. Please let us know, what do you think about our applications and methodology of innovation.